Lifting equipment, such as cranes, hoists, and forklifts, plays a critical role in various industries, from construction to manufacturing. However, improper use of this equipment can lead to serious accidents, injuries, or even fatalities. To ensure safe and efficient operations, there are four key requirements that must be considered when using lifting equipment. These requirements not only protect workers but also help maintain the integrity of the equipment and the load being handled.
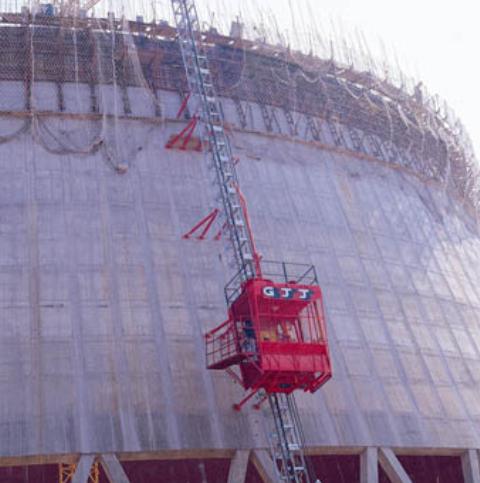
Proper Training and Certification
Why It Matters: Operating lifting equipment requires specialized skills and knowledge. Untrained or inexperienced operators are more likely to make mistakes that can result in accidents.
What to Do: Ensure all operators are adequately trained and certified to use the specific type of lifting equipment. Training should cover:
- Equipment operation and controls.
- Load capacity and limitations.
- Safety protocols and emergency procedures.
- Regular refresher courses to keep skills up to date.
Outcome: Well-trained operators reduce the risk of accidents and improve overall efficiency.
Equipment Inspection and Maintenance
Why It Matters: Lifting equipment is subject to wear and tear over time. Faulty or poorly maintained equipment can fail during operation, leading to catastrophic consequences.
What to Do: Implement a rigorous inspection and maintenance program:
- Conduct pre-use checks to ensure the equipment is in good working condition.
- Schedule regular maintenance by qualified technicians.
- Replace worn-out or damaged parts immediately.
- Keep detailed records of inspections and repairs.
Outcome: Regular maintenance ensures the equipment operates safely and extends its lifespan.
Load Capacity and Stability
Why It Matters: Overloading or improperly balancing a load can cause the equipment to fail, leading to dropped loads, structural damage, or tipping.
What to Do: Always adhere to the equipment’s rated load capacity and follow best practices for load handling:
- Know the weight of the load before lifting.
- Use appropriate slings, hooks, and rigging equipment.
- Ensure the load is balanced and securely attached.
- Avoid sudden movements or jerks during lifting.
Outcome: Proper load management minimizes the risk of equipment failure and ensures safe lifting operations.
Clear Communication and Worksite Safety
Why It Matters: Lifting operations often involve multiple workers, and miscommunication can lead to accidents. Additionally, a cluttered or unsafe worksite can increase the risk of incidents.
What to Do: Establish clear communication protocols and maintain a safe worksite:
- Use standardized hand signals or radio communication between operators and ground personnel.
- Designate a competent person to supervise lifting operations.
- Ensure the worksite is free of obstacles and hazards.
- Use barriers or warning signs to keep unauthorized personnel away from the lifting area.
Outcome: Effective communication and a safe worksite reduce the likelihood of accidents and improve coordination.
Conclusion
Using lifting equipment safely and effectively requires a combination of proper training, regular maintenance, careful load management, and clear communication. By adhering to these four key requirements, businesses can protect their workers, prevent equipment damage, and ensure smooth operations. Remember, safety should always be the top priority when working with lifting equipment. Regular audits and adherence to industry standards, such as OSHA or ISO guidelines, can further enhance safety and compliance.
Investing time and resources into these requirements not only safeguards your team but also contributes to the long-term success of your operations. Stay safe, stay compliant, and lift with confidence!